CNC Router: Difference between revisions
m German name with - |
migrated Kress CNC from mills and added content |
||
Line 85: | Line 85: | ||
# send the tool paths to the router in real time via the serial interface (USB) | # send the tool paths to the router in real time via the serial interface (USB) | ||
## options can be found under "[[G-Code Senders]]" | ## options can be found under "[[G-Code Senders]]" | ||
<br clear=all> | |||
== ?Kress CNC== | |||
[[User:sebastian|Sebastian]] bougt a sturdy homemade cnc router for cutting harder materials than the [[workbee]] is capable of. Also this | |||
{{MachineInfoBox | |||
|machine name=?Kress CNC | |||
|german= | |||
|image=Kress_CNC.jpg | |||
|synonyms= | |||
|type=CNC (subtractive manufacturing) | |||
|material=[[wood]], [[metal]] | |||
|location= | |||
|status=[https://github.com/comakingspace/do-something/issues/267|issue#267] | |||
|firmware= | |||
|software= | |||
|manual= | |||
|used with=[[endmills]] | |||
|similar=[[CNC Router|CNC router]] | |||
}} | |||
=== Workflow === | |||
'''This is just an overview and does NOT replace the [[CNC Router Introduction|personal introduction]]!''' | |||
# create the tool paths in a suitable CAM software (e.g. [[Fusion 360]]) | |||
## post and export the correct [[G-code]] flavor | |||
# [[CNC Router Workholding|secure your workpiece]] on the machine's bed | |||
## if you plan on cutting through the workpiece use a spoil board. | |||
# insert the appropriate collet & bit as defined in your tool paths | |||
# set your workpiece zero | |||
# put on [[PPE|personal protection]] and turn the spindle on | |||
# start your job from the USB stick | |||
=== Machine Control === | |||
The machine itself is mainly operated by the control panel located on the right side of the machine box and the jog-wheel: | |||
[[File:0 MainSwitch.jpg|thumb|left|The main switch turns on the power for the CNC, the spindle, light and the controller.]] | |||
[[File:1 Homing.jpg|thumb|left|Start by homing the machine. If the text „Reset“ blinks red on the screen, press the reset button (1). Press the “Origin Operation“ button (2). In the menu, select „Return To Home“ (3).]] | |||
Revision as of 18:51, 10 August 2022
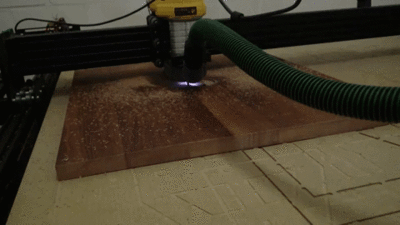
A CNC router is a computerized woodworking machine - basically a router mounted on a positioning system. While it may also be able to handle other materials than wood depending on the bits you use, a proper CNC mill is more precise for machining parts out of metals and other non-wood materials.
To use this machine, you need to familiarize yourself with at least two pieces of software:
- a CAD/CAM program (e.g. Fusion 360)
- may also be two different programs, one for CAD and one for CAM
- a G-Code sender
There is also an interesting new approach of handheld CNC routing coming out which may remove the size constraints that come with any fixed-frame machine.
Uses
You can make furniture or even build a house. For more ideas, check out the CNC Milling Ideas.
WorkBee
MachineInfoBox Ooznest WorkBee CNC | |
---|---|
Synonyms: | DE: CNC-Fräse, Portalfräsmaschine |
Material: | wood |
Used with: | 6 mm, 8 mm, 1/4" or 1/8" end mills; some kinds of router bits |
Access Requirements: | CNC Router Introduction |
Software: | LaserWeb, Fusion360, see G-Code Sender |
Firmware: | grbl |
Manual: | product page, click "documentation" tab |
Tutors: | NitramLegov Pakue Johannes Luzian Leo |
Similar (More or Less): | router, CNC mill |
We built the 1500mm x 1500mm version of the WorkBee CNC, which is based on the Openbuilds OX. It can currently cut sheet material of up to 50 mm thickness on a work area of approximately 1250 × 1250 mm. The surfaced (plangefräste) spoilboard area is 1260 × 1160 (x × y) mm.
Our plans for further improving it up can be found in our "WorkBee CNC" github project - maybe you would like to help?
Router
The router mounted to it is a Dewalt D26200 (GB; known outside Europe as DWP611). You need to consider the sizes of its collets (Spannzangen) when buying your router bits.
- no-load speed: 16000 - 27000 rpm
- max cutter diameter: 30 mm
- available collet diameters:
- 6 mm
- 8 mm
- 1/4 inch (6.35 mm)
- 1/8 inch (3.175 mm)
The collets of the DW613, DW620 and DW621 also fit the router and are easier to get in Germany than the original ones.
Spoilboard
Ooznest recommends a 6mm spoiler board, our first one is 20mm thick. It is mounted to the frame using 4 drop-in T-slot nuts. Cutting into the boards will make it uneven, from time to time it is neccessary to surface the spoiler board again.
The total size of the spoilboard is currently 1445 × 1370 mm.
When there is time, we would like to drill workholding holes into the spoilboard.
Electrics
(partially outdated - no dedicated CNC room since 2020!)
The spindle and the CNC controller (CNC xPro v3) + motors are hooked up to an electrical box on the left wall. You'll find a switch and an outlet for the spindle there. In case of an emergency the whole box can be shut off via one of the two emergency stops (inside the CNC room and on the outside above the access control). Everything except the Raspberry Pi will be turned off in that case.
The wiring of the CNC Controller board is as follows:
The wiring of the electrical box is as follows:
Dust Extraction
We have added a cyclone dust separator between the shop vac and the CNC router itself. Thereby, the bulk of the shavings and dust should be collected in an easily emptied box rather than the shop vac's bag.
The part that attaches the dust extraction hose to the router is called a "dust shoe". We are currently using this one designed by Patrick. The next version should ideally fit the dust extraction hose without an adapter and include a kind of transparent, flexible "skirt" to optimize the airflow.
Other interesting designs:
Workflow
This is just an overview and does NOT replace the personal introduction!
- create the tool paths in a suitable CAM software (e.g. Fusion 360)
- secure your workpiece on the machine's bed
- insert the appropriate collet & bit as defined in your tool paths
- turn the positioning motors on, home the machine and define the workpiece origin
- put on personal protection and turn the spindle on
- send the tool paths to the router in real time via the serial interface (USB)
- options can be found under "G-Code Senders"
?Kress CNC
Sebastian bougt a sturdy homemade cnc router for cutting harder materials than the workbee is capable of. Also this
MachineInfoBox ?Kress CNC | |
---|---|
![]() | |
Material: | wood, metal |
Used with: | endmills |
Access Requirements: | CNC Router Introduction |
Tutors: | NitramLegov Pakue Johannes Luzian Leo |
Similar (More or Less): | CNC router |
Workflow
This is just an overview and does NOT replace the personal introduction!
- create the tool paths in a suitable CAM software (e.g. Fusion 360)
- post and export the correct G-code flavor
- secure your workpiece on the machine's bed
- if you plan on cutting through the workpiece use a spoil board.
- insert the appropriate collet & bit as defined in your tool paths
- set your workpiece zero
- put on personal protection and turn the spindle on
- start your job from the USB stick
Machine Control
The machine itself is mainly operated by the control panel located on the right side of the machine box and the jog-wheel:
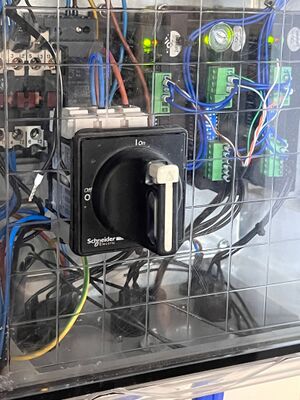
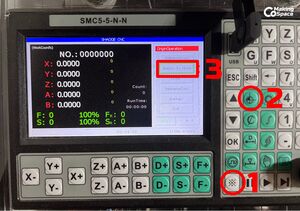
Tips & Tricks
- to avoid tear-out at the edge of a sensitive workpiece, it may be worthwhile to surround it with some sacrificial material (like MDF) before routing [1]
Materials
(For more details, see "Milling Experiences")
CNC routing is most appropriate for non-metal panels/boards. The exact material might dictate your choice of endmill or router bit!
Cutting certain metals, e.g. millable aluminum, may still be possible with a lot of extra work, but a rigid and liquid-cooled CNC mill would be the proper way to go.
Carbon Fiber
Carbon fiber (CF) dust can be harmful if handled improperly. If you intent to route CF parts on the CNC (like plates for quardrocopter parts) please follow the workflow below:
- Route carbon fiber only in a submerge water path e.g. in a large enough tray (keep enough towels near in case of an 'accident')
- Afterwards filter the water through a coffee filter or similar
- Don't vacuum the dust - instead, wipe it away with a moist towel or use some tape to pick it up
- Only wet sanding
- Keep the parts that came into contact with the carbon fiber dust in a sealed plastic bag until they are discarded
- Discard the remains at a local special waste disposal and don't put them in the garbage!
Helpful Links
- video tutorials:
- Ooznest YouTube channel (pretty new, but specific to our "WorkBee" setup)
- Fusion 360 CAM Tutorial for Beginners by Evan & Katelyn (insert our preferred G-code sender where they use Easel)
- other spaces with (somewhat) similar machines and good approaches/documentation:
- our page on choosing the proper feedrate