CNC Router: Difference between revisions
line break |
→G-Code Sender: renamed "workflow" and tried to make clearer |
||
Line 61: | Line 61: | ||
* https://www.thingiverse.com/thing:2802301 | * https://www.thingiverse.com/thing:2802301 | ||
=== G-Code | === Workflow === | ||
'''This is just an overview and does NOT replace the [[CNC Router Introduction|personal introduction]]!''' | |||
# create the tool paths in a suitable CAM software (e.g. [[Fusion 360]]) | |||
# [[CNC Router Workholding|secure your workpiece]] on the machine's bed | |||
# insert the appropriate collet & bit as defined in your tool paths | |||
# turn the positioning motors on, home the machine and define the workpiece origin | |||
# put on [[PPE|personal protection]] and turn the spindle on | |||
# send the tool paths to the router in real time via the serial interface (USB) | |||
## options can be found under "[[G-Code Senders]]" | |||
<br clear=all> | <br clear=all> |
Revision as of 15:36, 25 November 2018
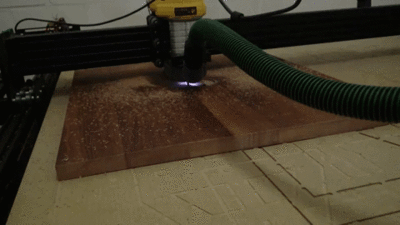
A CNC router is a computerized woodworking machine - basically a router mounted on a positioning system. While it may also be able to handle other materials than wood depending on the bits you use, a proper CNC mill is more precise for machining parts out of metals and other non-wood materials.
To use this machine, you need to familiarize yourself with at least two pieces of software:
- a CAD/CAM program (e.g. Fusion 360)
- may also be two different programs, one for CAD and one for CAM
- a G-Code sender
There is also an interesting new approach of handheld CNC routing coming out which may remove the size constraints that come with any fixed-frame machine.
Uses
You can make furniture or even build a house. For more ideas, check out the CNC Milling Ideas.
WorkBee
MachineInfoBox Ooznest WorkBee CNC | |
---|---|
Synonyms: | DE: CNC-Fräse, Portalfräsmaschine |
Material: | wood |
Used with: | 6 mm, 8 mm, 1/4" or 1/8" end mills; some kinds of router bits |
Access Requirements: | [[Needs Introduction::CNC Router IntroductionSome use of "" in your query was not closed by a matching "".]] |
Software: | LaserWeb, Fusion360, see G-Code Sender |
Firmware: | grbl |
Manual: | product page, click "documentation" tab |
Tutors: | NitramLegov Pakue Johannes Luzian LeoSome use of "" in your query was not closed by a matching "". |
Similar (More or Less): | router, CNC mill |
We built the 1500mm x 1500mm version of the WorkBee CNC, which is based on the Openbuilds OX. It can currently cut sheet material of up to 50 mm thickness on a work area of approximately 1250 × 1250 mm.
Details on setting it up can be found in issue #8 - maybe you would like to help?
Router
The router mounted to it is a Dewalt D26200 (GB; known outside Europe as DWP611). You need to consider the sizes of its collets (Spannzangen) when buying your router bits.
- no-load speed: 16000 - 27000 rpm
- max cutter diameter: 30 mm
- available collet diameters:
- 6 mm
- 8 mm
- 1/4 inch (6.35 mm)
- 1/8 inch (3.175 mm)
The collets of the DW613, DW620 and DW621 also fit the router and are easier to get in Germany than the original ones.
Electrics
The spindle and the CNC controller + motors are hooked up to an electrical box on the left wall. You'll find a switch and an outlet for the spindle there. In case of an emergency the whole box can be shut off via one of the two emergency stops (inside the CNC room and on the outside above the access control). Everything except the Raspberry Pi will be turned off in that case.
Dust Extraction
We have added a cyclone dust separator between the shop vac and the CNC router itself. Thereby, the bulk of the shavings and dust should be collected in an easily emptied box rather than the shop vac's bag.
The part that attaches the dust extraction hose to the router is called a "dust shoe". We are currently using this one designed by Patrick. The next version should ideally fit the dust extraction hose without an adapter and include a kind of transparent, flexible "skirt" to optimize the airflow.
Other interesting designs:
Workflow
This is just an overview and does NOT replace the personal introduction!
- create the tool paths in a suitable CAM software (e.g. Fusion 360)
- secure your workpiece on the machine's bed
- insert the appropriate collet & bit as defined in your tool paths
- turn the positioning motors on, home the machine and define the workpiece origin
- put on personal protection and turn the spindle on
- send the tool paths to the router in real time via the serial interface (USB)
- options can be found under "G-Code Senders"
Tips & Tricks
- to avoid tear-out at the edge of a sensitive workpiece, it may be worthwhile to surround it with some sacrificial material (like MDF) before routing [1]
Spoilboard
Ooznest recommends a 6mm spoiler board, our first one is 20mm thick. It is mounted to the frame using 4 drop-in T-slot nuts. Cutting into the boards will make it uneven, from time to time it is neccessary to surface the spoiler board again.
When there is time, we would like to drill workholding holes into the spoilboard.
Materials
(For more details, see "Milling Experiences")
Plastics
Polycarbonate works better than acrylic glass.
POM/Acetal/Delrin
Bits
tested with 2 and 3 sided HSS Bits 4mm-6mm but no indication against any other diameters
RPM, Speeds, etc.
Spindle on level 1 (=16 000rpm)
- Schnittvorschub: 500mm/min +
- Einfahrvorschub: 500mm/min +
- Ausfahrvorschub: 500mm/min +
- Helixvorschub: 200mm/min +
- Eintauchvorschub: 30mm/min
- Depths: 2-3mm
Strongly advise a horizontal Rohteilaufmaß and a final finishing cut to remove any "layer" marks.
Cooling
Not neccessary with the current settings but might increase the cutting speeds drastically
Plywood
Most kinds of plywood should work, but of course you only get out what you put in - Micha has had bad experiences with pine plywood as it is much too soft and likes to warp.
Aluminum
Possible with a lot of patience and the correct bits, but check if it's millable aluminum
- different alloys of aluminum containing Cu, Si, Pb
Bits
maximum two cutting sides carbide is more rigid than HSS and advised by some online guides Tested 4mm 2-sided pointy-end bit with acceptable success
RPM, Speeds, etc.
Values are only the tested ones, faster CAN be possible as well
- slow RPM: 16 000 is our minimum but e.g. for a 4mm bit, 6000 RPM would be better
- different mill or PID-ing?
- Feed Rate/Schnittvorschub: ~200 mm/min
- Einfahrvorschub: 15-20 mm/min
- Ausfahrvorschub: 200 mm/min
- Helixvorschub: 15-25 mm/min
- Eintauchvorschub: 15 mm/min
- Depths: 0.25mm per pass
Milling directions (to be tested): Conventional/Up-Cut (Gleichlauf) milling milling for the basic different passes with a finish using Climb-milling/Down-Cut milling (= Gegenlauf)
Cooling
Not yet tested
- any sort of lubricant or coolant will increase the efficiency of aluminum milling
- there are suggestions ranging from cutting fluid over WD-40 to candle wax for lubing
- As coolant, a water or alcohol mist seems unsuitable with our pressboard
- instead, using the air compressor might be a possiblity
Helpful Links
- video tutorials:
- Ooznest YouTube channel (pretty new, but specific to our setup
- other spaces with (somewhat) similar machines and good approaches/documentation:
- Feeds and Speeds Calculator